Busbar Processing Automation: Powering the Future of New Energy Vehicles
In the fast-evolving landscape of new energy vehicles (NEVs), efficiency, precision, and innovation are driving forces behind progress. Central to this revolution is busbar processing automation, a transformative technology reshaping the production of vital components that power electric and hybrid vehicles. This article delves into what busbar processing automation entails, its significance in the NEV sector, and how Wanfur Industry Co., Ltd. is leading the charge toward a sustainable future.
1. Introduction to Busbar Processing Automation
Understanding Busbar Processing Automation
Busbar processing automation involves the use of cutting-edge machinery and robotic systems to streamline the production of busbars—conductive metal bars, typically crafted from copper or aluminum, essential for distributing electrical power in NEVs. These components undergo complex processes such as cutting, punching, bending, peeling, and welding, all of which demand high precision. Historically, these tasks relied on manual labor, which was time-consuming and susceptible to errors. Automation changes the game by delivering unmatched accuracy and efficiency.
The global electric vehicle market is booming, with Statista projecting it to hit USD 828.6 billion by 2025, boasting a compound annual growth rate (CAGR) of 6.95% from 2025 to 2029. This surge fuels the need for advanced manufacturing solutions, positioning automation as a critical tool for staying ahead. Curious about industry trends? Check out our latest posts for more insights.
The Role in New Energy Vehicles
In NEVs, busbars are the lifeline, channeling power from batteries to systems like motors, lights, and electronics. Their quality directly affects vehicle efficiency, safety, and durability. Manual methods once sufficed, but today’s demand for mass production and flawless precision outpaces human capabilities. Automation ensures each busbar meets stringent standards, slashing waste and speeding up timelines—vital as NEVs are expected to claim 30% of global vehicle sales by 2030.
This shift isn’t just about technology; it’s about scalability. As the NEV market grows, manufacturers need solutions that keep pace without sacrificing quality, making busbar processing automation indispensable.
2. Wanfur Industry Co., Ltd.: Pioneering Automation for Green Mobility
About Wanfur Industry Co., Ltd.
For over 15 years, Wanfur Industry Co., Ltd. has been a trailblazer in busbar processing automation. Based in China, we specialize in fully automated solutions customized for the NEV industry’s unique demands. Our track record has earned us partnerships with leading manufacturers globally, cementing our role in the green mobility revolution. Learn more about our journey on our company pages.
“Automation is the backbone of sustainable manufacturing,” says Jane Smith, a renowned automation expert. “Companies like Wanfur are setting the standard for efficiency and innovation in the NEV space.”
Our Vision and Mission
Our mission is clear: to spearhead green mobility by providing state-of-the-art automation technology that boosts efficiency, quality, and sustainability in NEV production. We aim to push innovation boundaries, ensuring our clients meet rising eco-friendly vehicle demand without compromising performance or cost. This vision drives every solution we develop, from concept to execution.
Explore Our Cutting-Edge Products
Wanfur’s product portfolio tackles every facet of busbar processing. Here’s a glimpse at our flagship offerings, showcased in a carousel below:
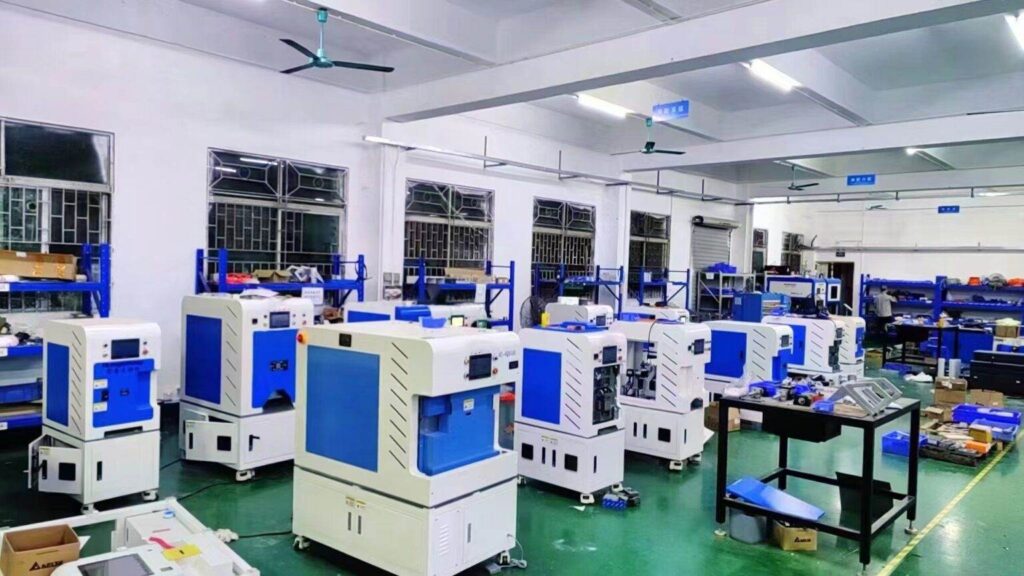
Busbar Peeling Machine: Strips hard glue from copper bars in 15 seconds, preserving surface integrity.
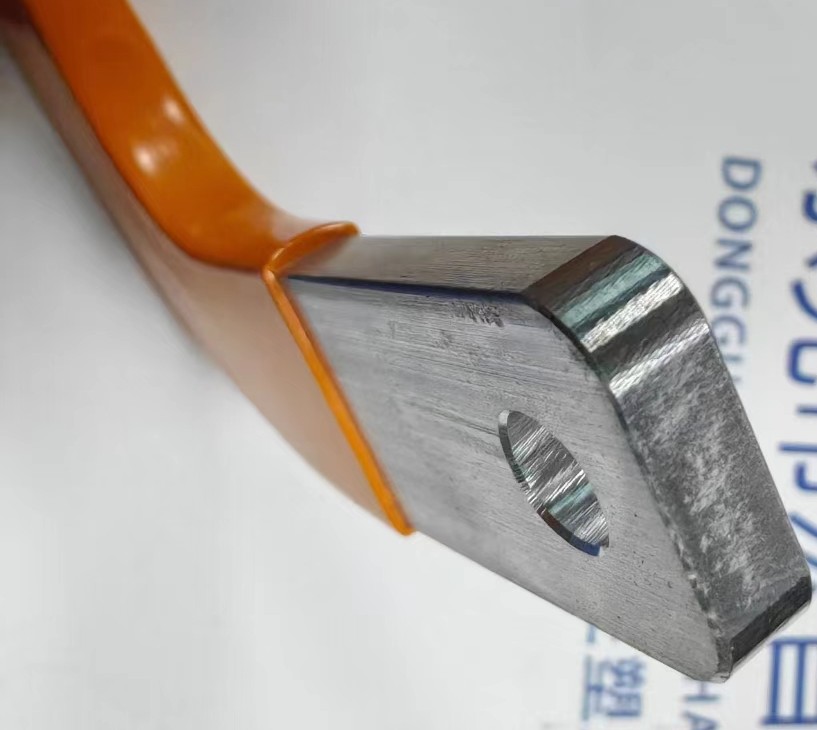
Busbar Milling Machine: Delivers precise milling for seamless electrical connections.
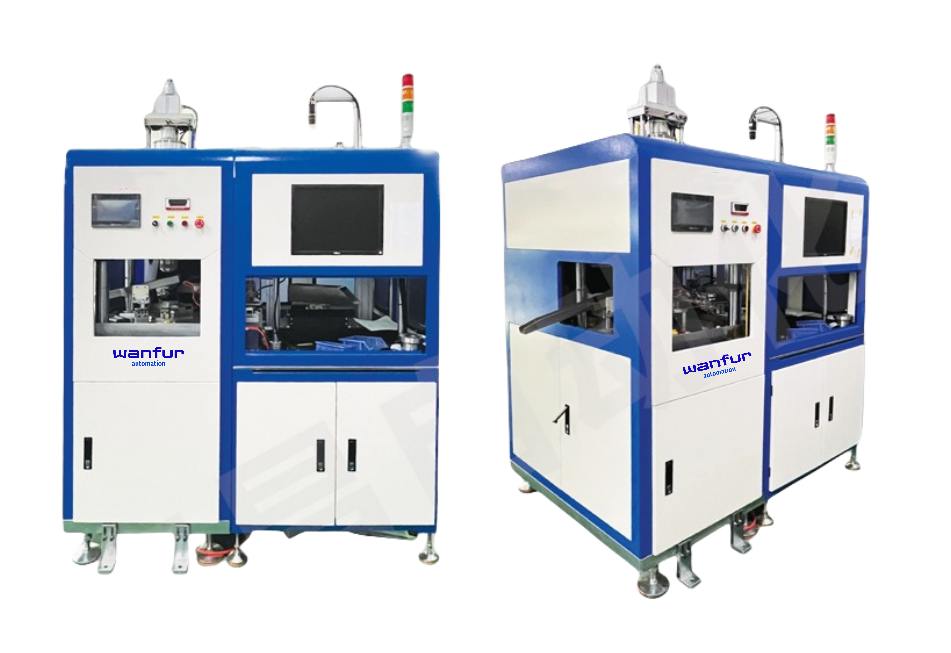
Metal Vibration Welding Machine: Ensures robust welds for durable busbar assemblies.
Beyond products, we offer 24/7 customer support and bespoke R&D services. Whether upgrading an existing line or starting anew, explore our automation solutions to see how we can help.
3. Key Benefits of Busbar Processing Automation
Supercharging Production Efficiency
Automation turbocharges efficiency, a standout benefit for NEV manufacturers. Take our Busbar Peeling Machine—it strips a copper bar in just 15 seconds, a feat that dwarfs manual efforts. This speed boosts output, enabling tighter deadlines and scalable production. Industry stats back this up: automation can lift production rates by 20% by cutting downtime and optimizing workflows (Productivity.com).
In the NEV race, where speed to market is king, this efficiency edge is transformative. Discover more benefits in our automation categories.
Precision That Powers Performance
Precision is critical in busbar manufacturing—tiny flaws can trigger electrical failures, jeopardizing vehicle safety. Automation eliminates human error, ensuring every busbar aligns with exact specs. Studies reveal automation slashes defect rates by up to 30%, enhancing component quality and reducing recalls. Our machines, equipped with advanced sensors and robotics, guarantee precision at every step.
Driving Down Costs
Though automation requires upfront investment, the long-term savings are substantial. It cuts labor costs, reduces waste, and accelerates production, offering a strong ROI. Automated systems also demand less maintenance, trimming operational expenses. Per OptiProERP, the automation market is set to soar from USD 191.74 billion in 2021 to USD 355.44 billion by 2028, fueled by these cost benefits.
Safety First
Handling heavy materials and machinery poses risks to workers. Automation takes on these hazards—lifting, cutting, welding—enhancing workplace safety. Our robotic systems minimize operator exposure, aligning with safety standards and reducing accident risks.
Stay tuned for the second half, where we’ll explore challenges, case studies, and future trends in busbar processing automation!